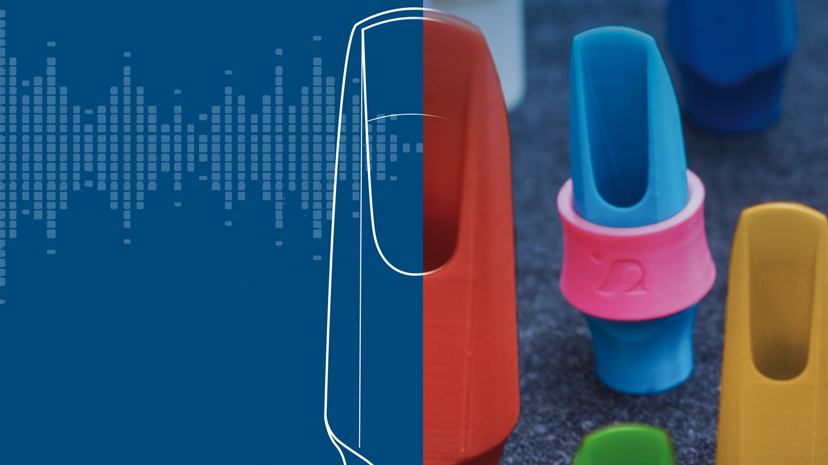
IF WE tailor-make musical instruments, can we help musicians deliver a personalized sound?
Each musician aims to cultivate his art in order to be unique. Its aesthetic sound constitutes its identity.Is the answer to customize an instrument for each artist ? Can an instrument’s design influence its sound identity ?And can we industrialize custom-made instruments to make them accessible to every musician?
Syos is an emerging company that offers musicians the highest level of customization you can think of: the possibility to shape their own sound.
Just as singers have their unique voice, with Syos musicians can shape their sound.
Applying scientific expertise from their five years of research at prestigious laboratories including Ircam and McGill University, Syos’s founders developed an algorithm that links the vocabulary a musician uses to describe his dream sound to create the geometry for a musical instrument to obtain this specific sound. 3D printing then manufactures that unique piece in a quick, flexible and personalized way, at a moderate cost.
The project was launched in 2014 and the company created in 2016. The Syos team has won multiple prizes and grants. They have more than 150 customers in several countries in Europe and North America, and famous saxophone players have adopted their products.
Syos’s success comes from putting the musician is at the heart of the design process. Their unique algorithm translates a musician’s words about their ideal sound into an instrument geometry to deliver the specific sound. Instead of mass-producing standardized instruments, Syos create unique pieces to to meet the expectations of each of their customers. They currently support the saxophone and clarinet, with plans to expand to other instruments.
3D printing technology enables easy manufacture of innovative geometries, with acoustic improvements, which simply cannot be built with traditional processes such asplastic injection or CNC. It also outclasses handmade production since the 3D design-to-3D printing process is repeatable , allowing great control and prediction of the output quality.
The result? The mass-market can experience a degree of personalization previously only possible with expensive hand-made production that was reserved for an elite population.
GOAL 12: Responsible consumption and production
Syos ensures sustainable consumption and production patterns. This new way of building instruments is possible thanks to the use of a knowledge- driven 3D parametric design approach coupled with 3D printing.
Syos joined the 3DEXPERIENCE Lab in 2017. Being part of the program gives them access to the cloud-based 3DEXPERIENCE platform and Dassault Systemes mentors. This combination is empowering Syos to:
Pauline and Maxime put the alliance of acoustic and cognitive sciences at the service of music.
They´re talking about us
Do you think your project is the next big thing?
Join the team !